Bulk Commodity
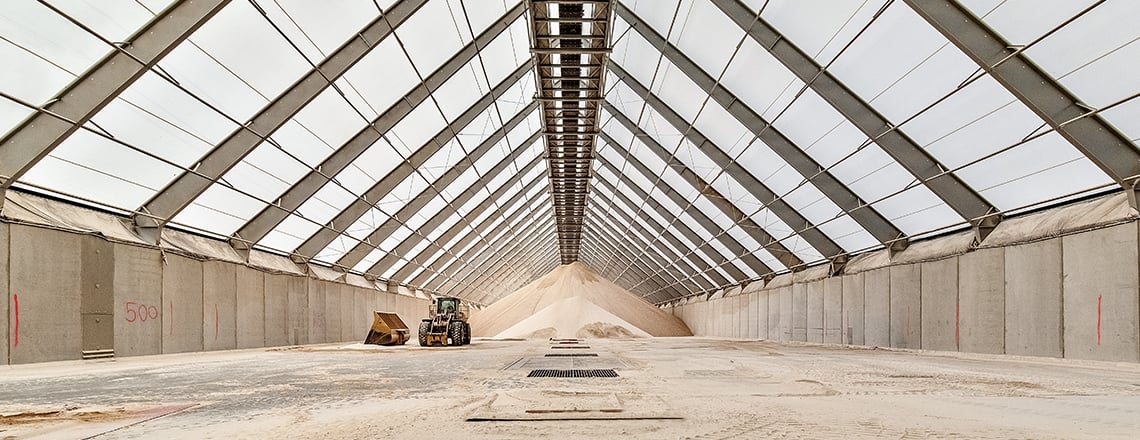
Custom Storage Solutions for Salt, Sand, Fertilizer & Bulk Materials
Maximizing space, protecting materials, and maintaining efficiency are critical in bulk commodity handling—all while controlling costs. Whether you're an architect, contractor, or business owner, the right storage facility is essential.
Our salt storage buildings are engineered to protect against moisture and corrosion, while our sand storage structures maximize capacity with clear-span designs. We design within your specific material handling requirements, from fertilizer storage buildings to specialized frac sand storage facilities.
Legacy’s custom fabric buildings offer flexible, cost-effective, and durable storage for grain, aggregates, fertilizer, and more.
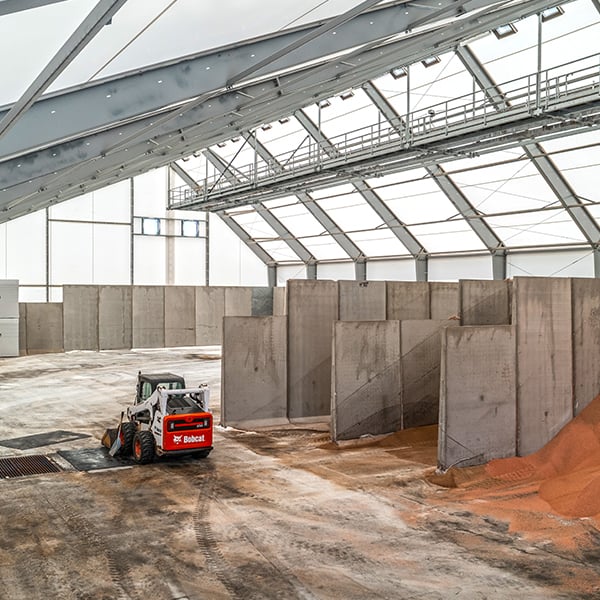
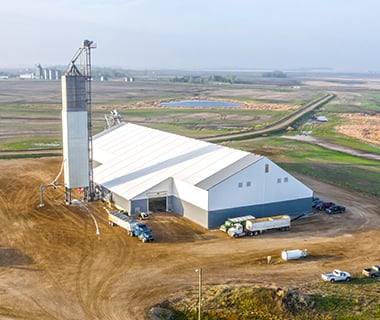
Emphasize Efficiency
Our buildings are engineered to meet the unique demands of bulk commodity storage, offering unobstructed interiors for higher storage capacity, rapid installation to minimize downtime, moisture and corrosion resistance to protect materials from weather damage and contamination, and cost-effective construction.
With a focus on efficiency, protection, and customization, our structures keep your bulk operations running smoothly.
HOW LEGACY FABRIC CAN HELP
Maximized Storage & Efficiency
Bulk material storage requires open, adaptable space for efficient handling, transport, and processing. Our clear-span interiors eliminate structural obstructions, giving you higher stacking capacity for better space utilization, room for conveyors, loaders, and heavy equipment, and adaptability for multiple commodities over time.
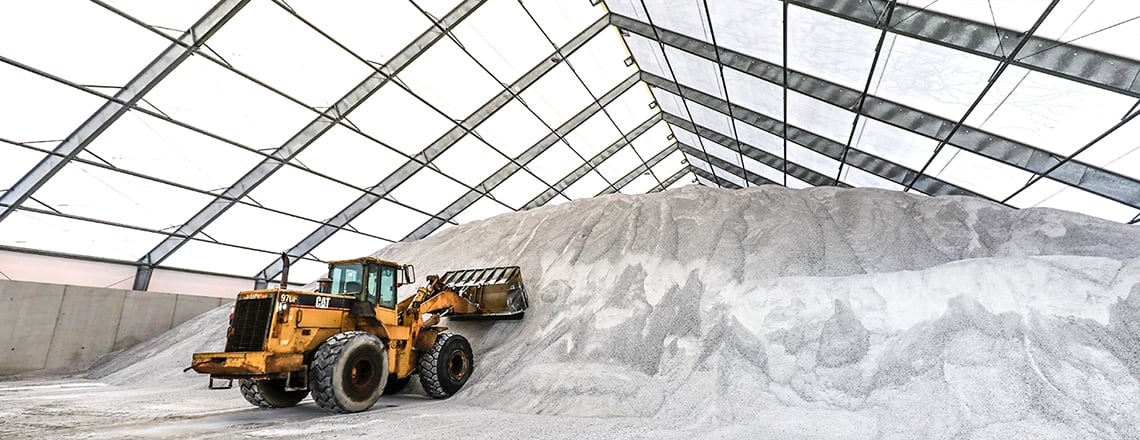
Faster Construction, Faster ROI
Waiting months for a storage facility isn’t an option when demand fluctuates and supply chains are tight. Our pre-engineered buildings cut construction time by weeks or months compared to conventional options—helping you expand storage capacity without disrupting operations.
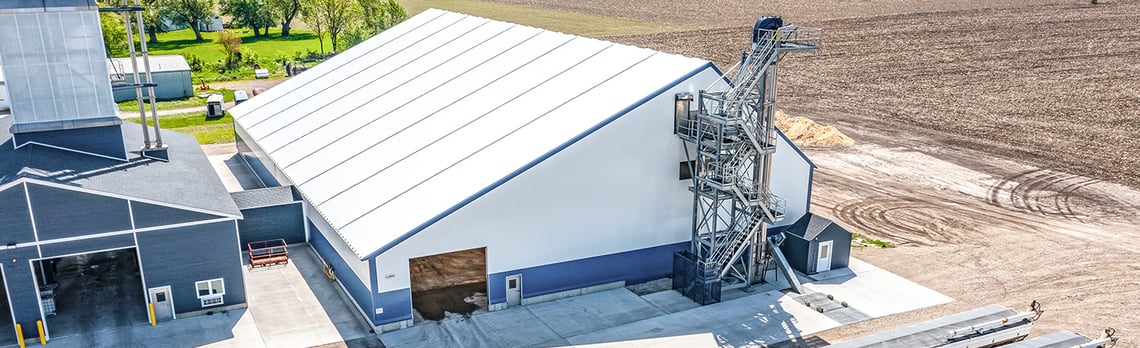
Protect Your Bulk Materials from the Elements
Salt storage buildings require special consideration for corrosion resistance, while fertilizer storage buildings need precise climate control to maintain product integrity. Our fabric structures address these challenges with superior moisture resistance and ventilation options tailored to your specific materials.
Tension fabric cladding resists moisture and prevents condensation buildup, reducing rust and corrosion over time. Ventilation and climate control options also ensure consistent interior conditions.
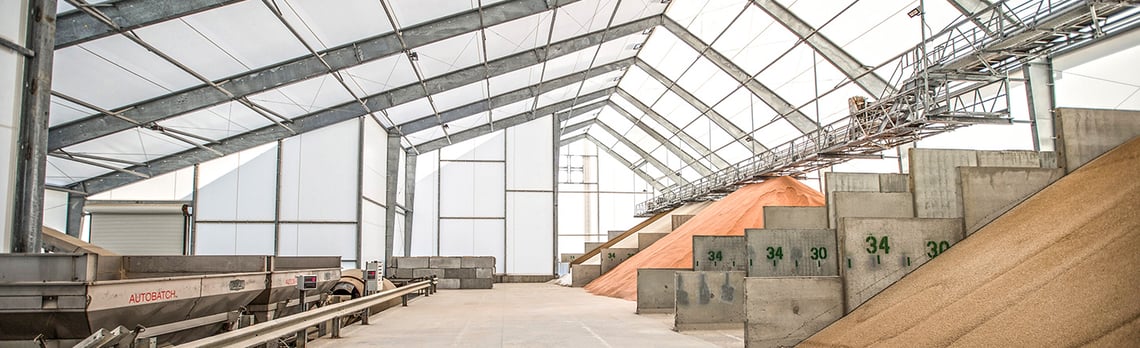
Built for Cost Efficiency & Long-Term Performance
Traditional bulk storage buildings come with high material costs, long lead times, and expensive maintenance. Our fabric structures deliver the strength and performance you need—at a fraction of the cost. Lower construction expenses with lightweight, engineered materials, reduce energy costs with natural daylighting and optional insulation, and limit maintenance for a longer-lasting, more reliable structure.
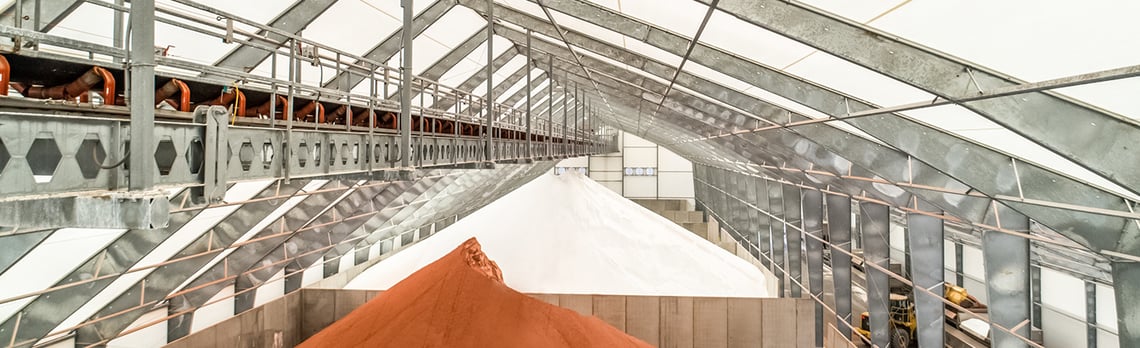
OUR PROCESS
Your dedicated project manager ensures every stakeholder's needs are met—from architectural vision to installation practicality—keeping your project on schedule from day one.
Our in-house engineering team works directly with designers and manufacturing, resolving potential issues before they become costly delays. This means faster approvals and fewer change orders, saving you both time and budget.
Every component of your building is manufactured in our 87,000 sq ft facility in St. Cloud, MN, under rigorous quality controls. This eliminates supply chain delays and ensures every component arrives on-site ready for installation.
Whether you opt for expert oversight of your local crews or our full-service installation team, you get our proven safety protocols and quality guarantees. Both options include on-site support to ensure your building is completed to specification and on schedule.
REAL-WORLD SUCCESS IN BULK STORAGE
Custom Fabric Structures for Agriland FS Woodbine
19,404 sq ft Fertilizer Storage Building | Woodbine, IA
Discover Legacy's fabric building design for Agriland FS Woodbine's fertilizer storage. Download the case study to explore this innovative project!
View Case Study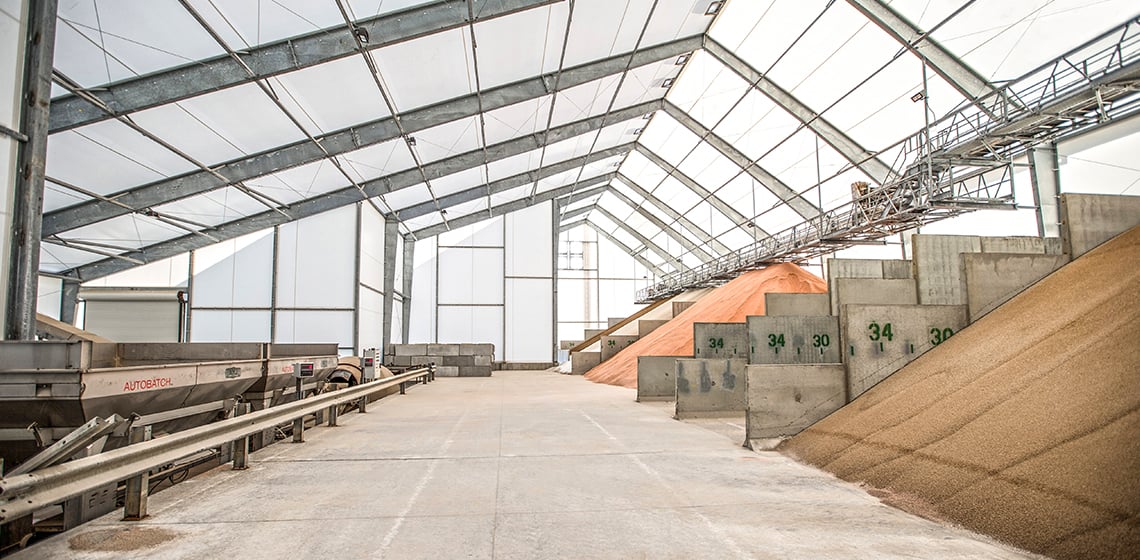
Feed Products & Bulk Feed Storage
62,800 sq ft Bulk Feed Storage Building | Madison, IL
Feed Products and Service expanded their Madison, IL location with a fabric structure to store and distribute bulk animal feed due to business growth.
View Case Study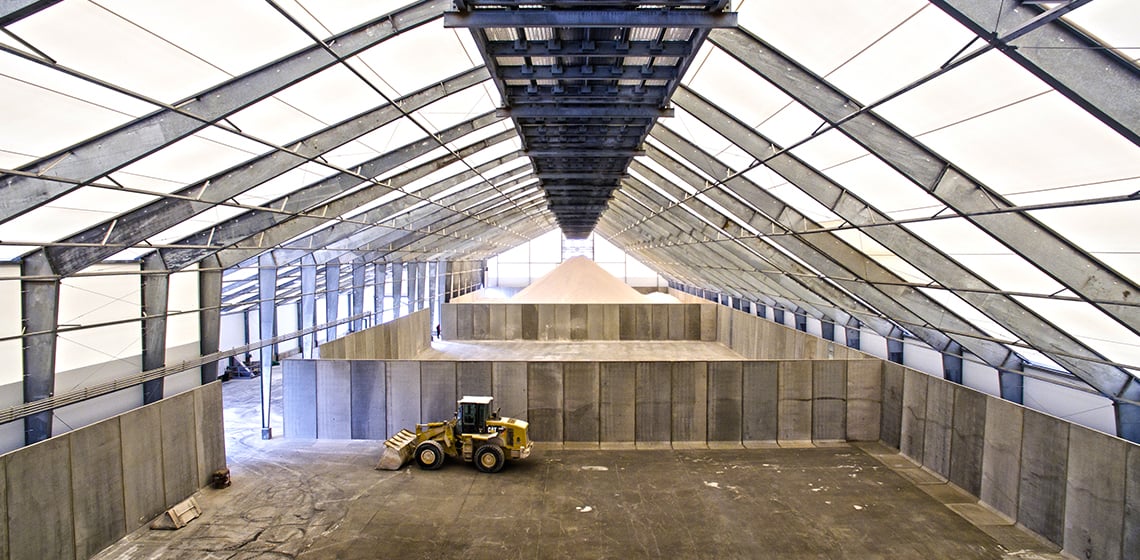
Fertilizer Storage Building for Northern Farmers Co-op
14,616 sq ft Fertilizer Storage Building | Williams, MN
Northern Farmers Co-op Fertilizer Storage: Custom fabric buildings for efficient storage. Explore our innovative design options.
View Case Study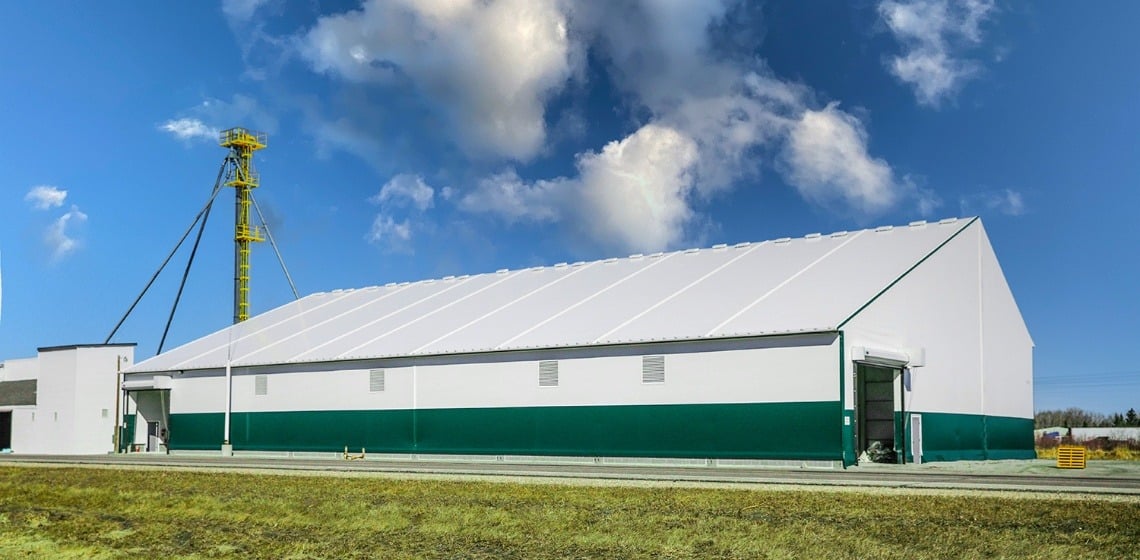
Gunther Salt Company Salt Storage Building
28,080 sq ft Commercial Salt Storage Building | St. Louis, MO
Gunther Salt Company built a new storage facility in St. Louis for agricultural salt mix, arriving by barge and loaded onto trucks via conveyor.
View Case Study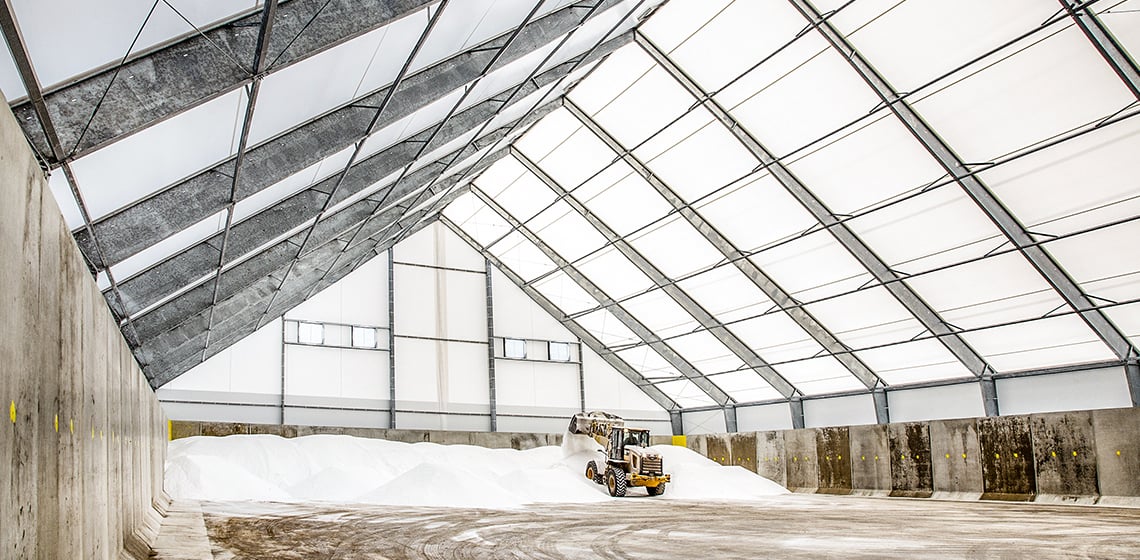
IEI Barge Services Storage Building
63,010 sq ft Tension Fabric Building for Fertilizer Storage and Blending | East Dubuque, IL
In 2015, IEI Barge Services chose Legacy’s lightweight design for a fertilizer storage building, solving soil and corrosion challenges affordably.
View Case Study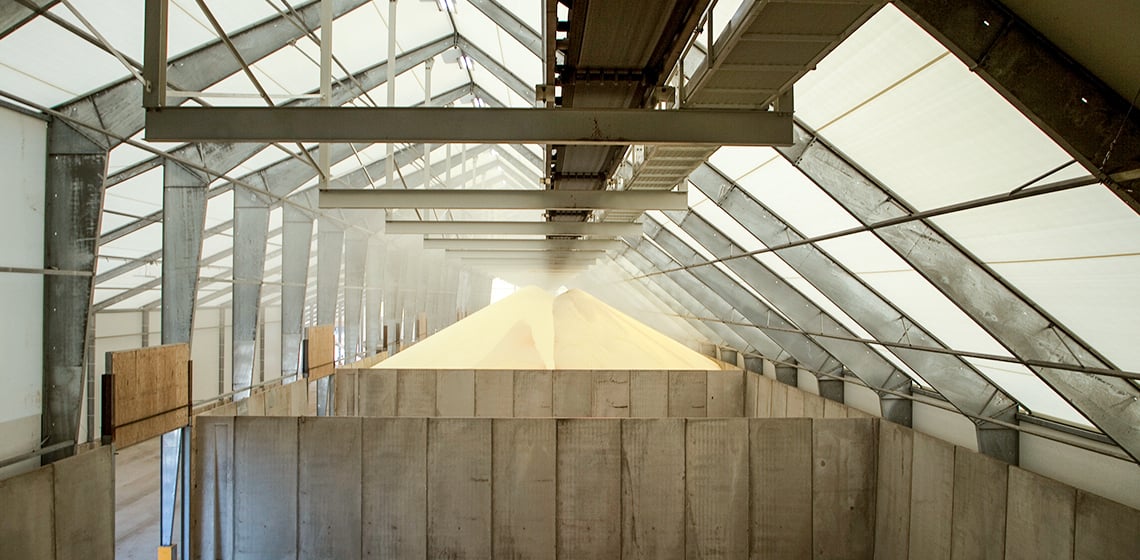
Tronson Grain Fertilizer Storage
37,200 sq ft Fertilizer Storage
Legacy built a fertilizer storage facility for Tronson Grain in Crary, ND, with multiple bins and a 150-ton automated loading and mixing system.
View Case Study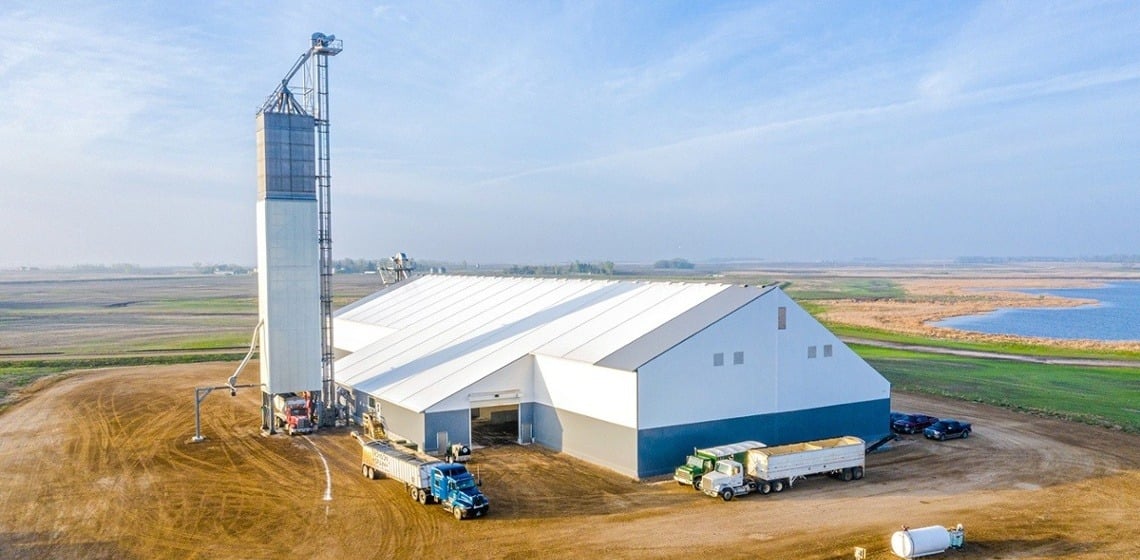
Versatile Transload Building Solutions for Bulk Commodity
101,520 sq ft Salt Storage + Distribution at a Railroad Transload Facility
Vermont Railways, Inc. was looking to develop a new state-of-the-art rail-to-truck transload building to efficiently handle bulk commodities
View Case Study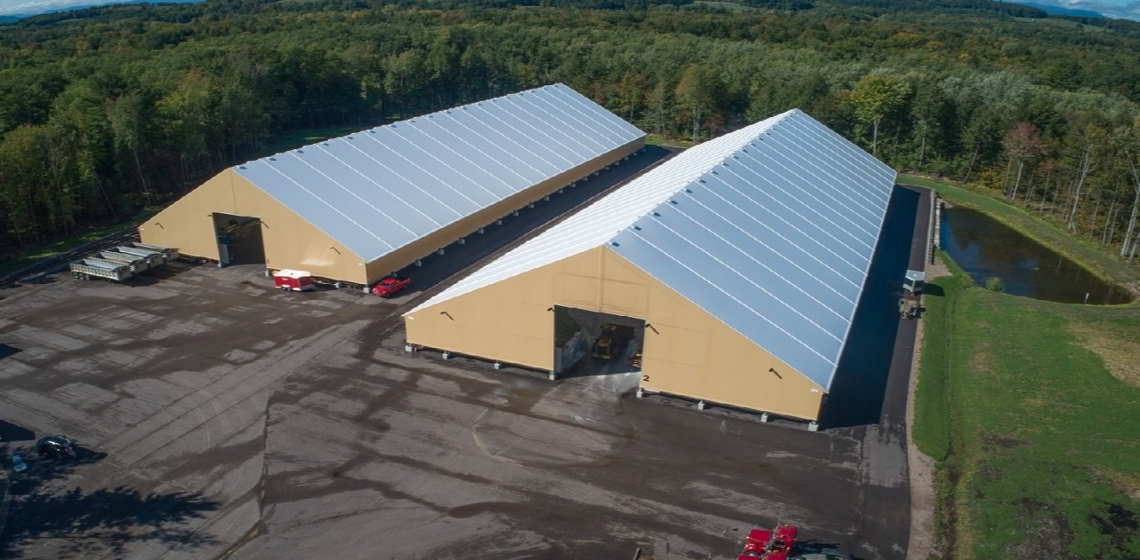
Smithfield Bulk Feed Storage Structure
60,000 sq ft Flat Feed Storage
The largest hog producer and processor increased their feed manufacturing system with a tension fabric building.
View Case Study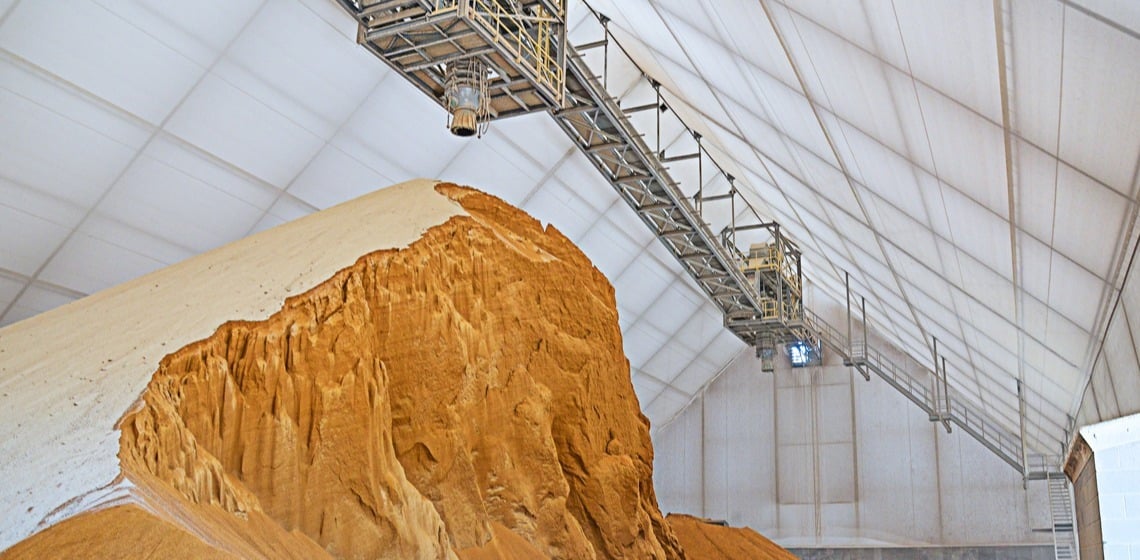
Hull Coop
18,900 sq ft Fertilizer Storage Facility | Hull, IA
Hull Coop’s fabric building by Legacy delivers durable, weatherproof bulk storage, maximizing efficiency and protecting products from the elements.
View Case Study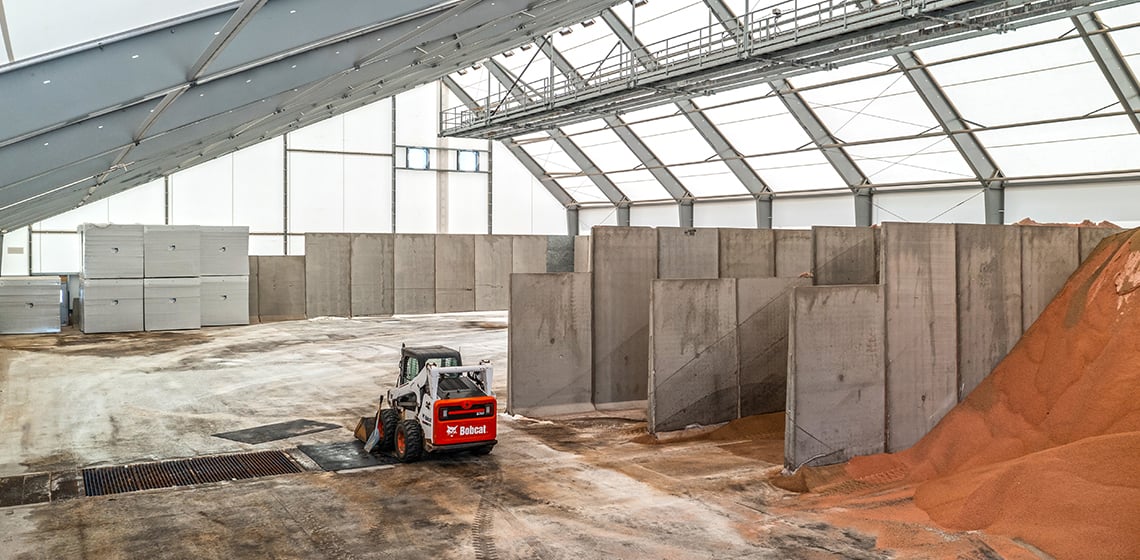
Montgomery County Salt
18,400 sq ft Municipal Salt Storage
Legacy built a salt storage facility in Gaithersburg, MD, with a 21-ft wall and EpoxxiShield™ COR Pro finish to protect frames from salt corrosion.
View Case Study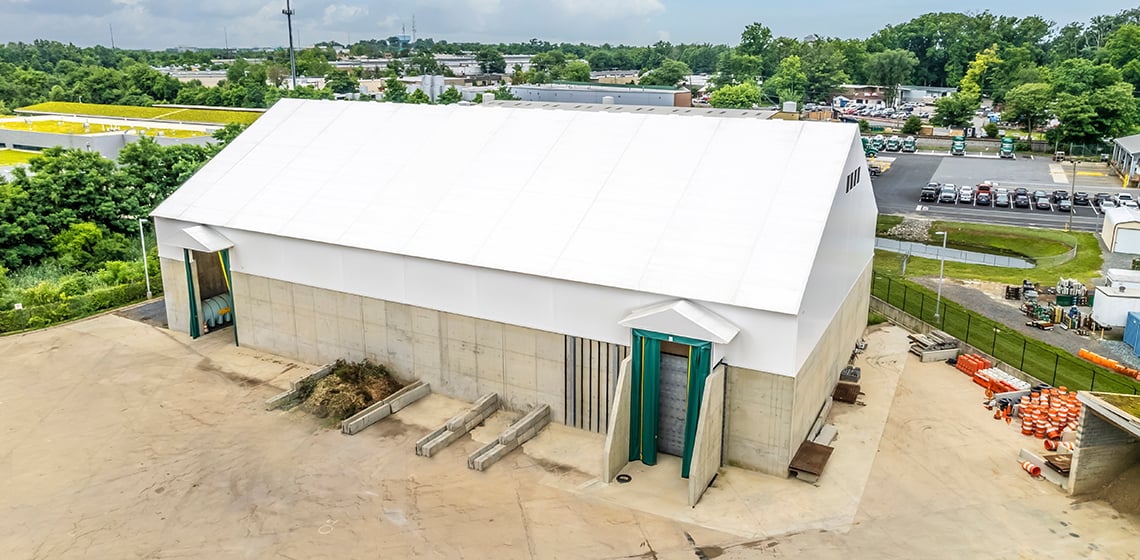
Paul Meyer Chemicals
10,080 sq ft Fertilizer Storage Facility
Legacy built a fertilizer facility in Walcott, IA, with overhead coil doors, conveyor support, and durable ExxoTec™ cladding.
View Case Study
The DeLong Company, Inc.
69,600 sq ft DDGS Storage Facility
The DeLong Company and Legacy built a 69,600-ft DDGS export facility, opening Wisconsin to new agricultural markets.
View Case Study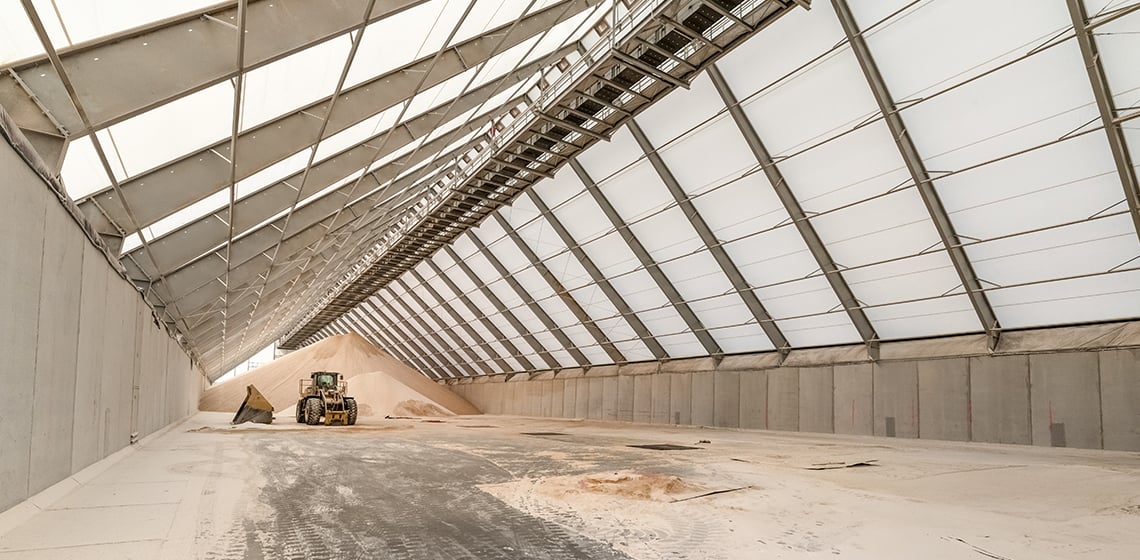
Testimonials
Everything that Legacy said they were going to do, they did.
We obviously had contracts, but the overall feel was kind of like the olden days, where you felt you could just take somebody at their word. Price is a major factor in any purchase decision. But we didn't blink at having to pay a little more for the Legacy structure. Sometimes you have to spend more to get a higher quality building. The installation was very smooth. Legacy's in-house crew worked in cold winter conditions, and they erected the building within five days. They were a very professional group, and I'd highly recommend them. We like the sidewall columns going straight up instead of curving down like in our hoop buildings. First off, it lets us put more product in there. And our front-end loaders can get much closer to the walls and drive straight down the sides. It gives us more working room and increases our efficiency. In the long run I think this will be a building that requires less maintenance. Legacy was so outstanding to work with that I didn't even bother looking at pricing elsewhere.
The new building will protect the salt supply.
It will be protected from being compromised by wind and precipitation. Once the general contractor completed the footings and floors, Legacy installed the fabric building very quickly, in about two weeks. It was a very positive process with professional communication between Legacy and Dewberry throughout the project.
The Legacy construction crew was very professional and courteous.
Because of our soil issues, we simply couldn't afford to construct a more traditional building. The concrete costs made a more traditional building cost prohibitive. The lightweight design of our Legacy building allowed us to reach a compromise between soil conditions and cost. Regarding the design and construction phases of the building, I can say that the process went exceptionally well. When I made eleventh-hour changes to the job, Legacy handled them with ease. They finished the job well ahead of schedule, worked safely, and followed our stringent safety requirements to the letter.
Start Your Project
Turn Your Vision into Reality—Faster
Get expert guidance on your facility design, timeline, and budget. Our team will help you reduce construction time, lower ongoing operational costs, and meet all environmental and safety requirements.