Oil, Gas, & Energy
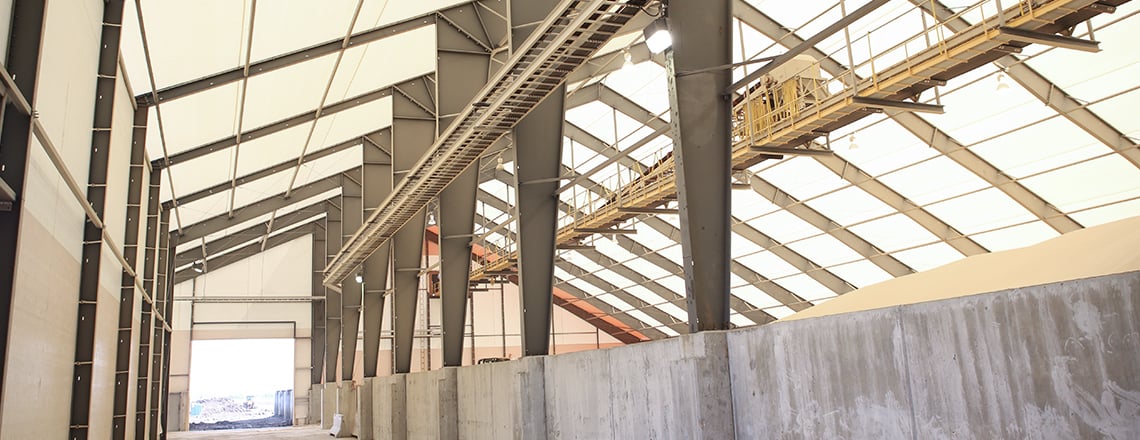
Stronger, Faster, Smarter Oil & Gas Projects Start Here
From processing facilities to storage terminals and equipment enclosures, every structure in the oil & gas industry needs to withstand harsh conditions, tight deadlines, and evolving regulations.
Whether you're designing, building, or managing these projects, you need a reliable, adaptable solution that works as hard as you do.
From oil storage facilities to gas storage installations, our custom fabric buildings deliver protection and security for your most valuable assets and operations.
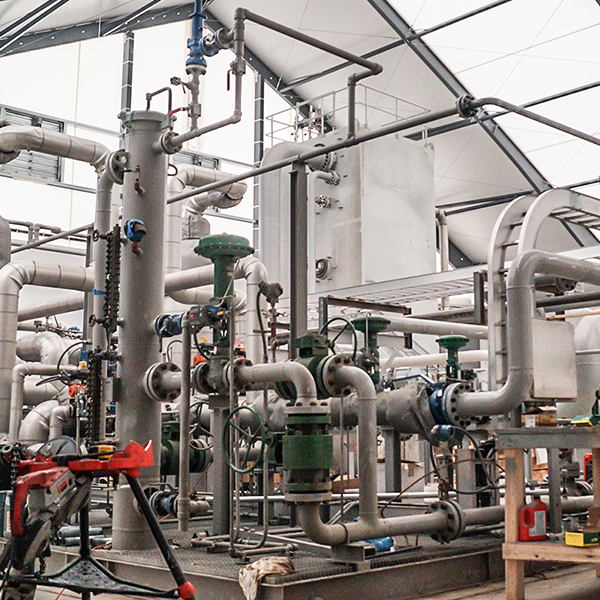
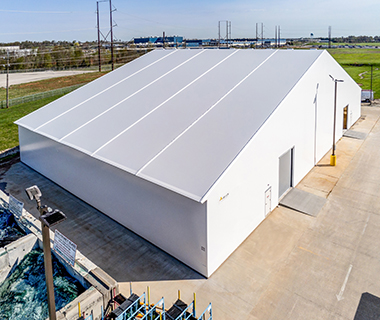
Adapt to Extreme Conditions
From design to installation, every decision in an oil & gas project impacts safety, efficiency, and long-term performance. Beyond durability, you’re also balancing tight budgets, evolving safety regulations, and high-stakes timelines. A single delay or miscalculation can have costly consequences.
That’s why leading architects, contractors, and business owners are turning to innovative building solutions that offer durability without delays. Legacy structures are engineered for the realities of your job site—built to withstand extreme conditions, streamline construction, and deliver lasting value.
HOW LEGACY FABRIC CAN HELP
Faster Construction, Minimal Downtime
Traditional building methods often mean long lead times, material shortages, and disruptive on-site construction. Legacy’s pre-engineered fabric structures arrive ready for rapid installation, cutting construction time. With fewer materials and no need for interior support columns, we simplify logistics—so you can get operations up and running faster without sacrificing quality.
.jpg?width=1140&height=440&name=IMAG2695%20(1).jpg)
Strength Built for Harsh Environments
From scorching heat to subzero temperatures, oil & gas structures face some of the toughest conditions in any industry. Our high-tensile fabric is UV-resistant, corrosion-resistant, and designed to perform in extreme environments. Paired with a durable steel frame, Legacy buildings provide long-term reliability without the risk of rust, rot, or degradation—ensuring your investment lasts for decades.
Besides sheltering key processing equipment and processes, our buildings can serve multiple additional activities:
- Vehicle and equipment storage
- Maintenance shops
- Warehouses
- Mechanical facilities
- Treatment applications
- Climate-controlled indoor applications
- Oil storage facilities with secondary containment options
- Gas storage structures with enhanced ventilation systems
- Temporary or permanent oil and gas storage solutions
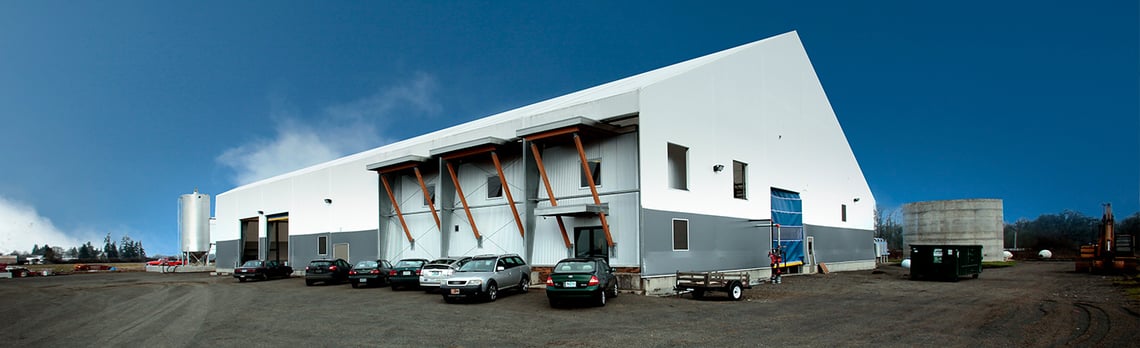
Flexible, Customizable Designs
No two projects are alike, which is why our structures are designed for maximum adaptability. Need a large clear-span interior for equipment storage? Or a ventilated enclosure for hazardous material handling? Legacy buildings can be customized with features like insulation, ventilation systems, lighting, and specialty doors to meet the unique demands of your site—without the cost and complexity of traditional construction.
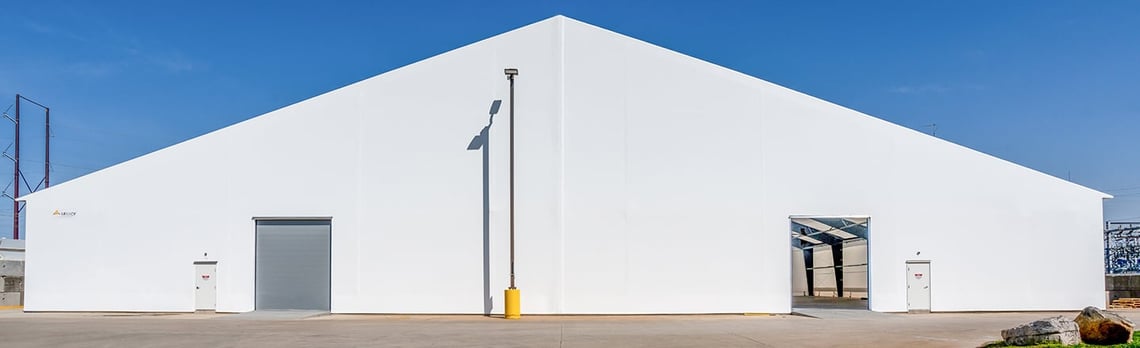
Regulatory Compliance & Safety Assurance
Staying compliant with OSHA, EPA, and local building codes can be a challenge, but our structures are engineered with safety and compliance in mind. Whether you need a fire-retardant fabric, natural daylighting to reduce energy consumption, or advanced ventilation systems to manage hazardous materials, we’ll ensure your building meets all requirements—giving you peace of mind from day one.
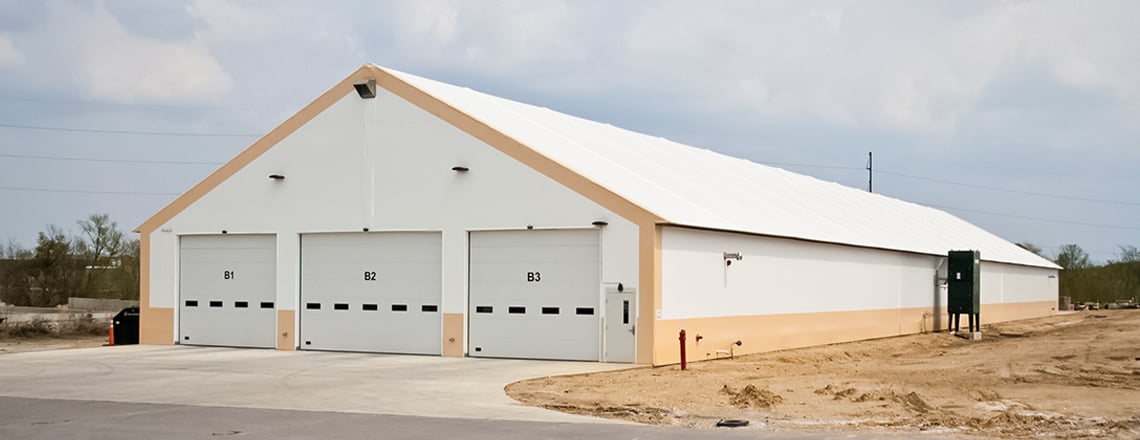
Lower Lifetime Costs, Maximum ROI
Unlike traditional steel or wood structures, Legacy fabric buildings require less maintenance, reducing the need for costly repairs and corrosion treatments. The energy-efficient design also reduces heating and cooling costs, while the modular construction allows for easy expansions as your needs grow. That means a lower total cost of ownership and a higher return on investment over time.
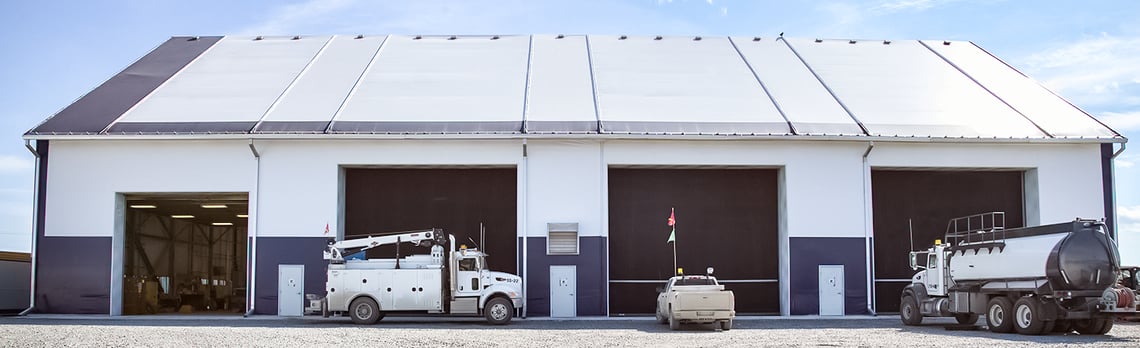
Specialized Solutions for Oil and Gas Storage
Whether you need oil storage facilities that meet strict safety regulations or gas storage structures built to handle volatile materials, our buildings are engineered specifically for the energy sector. Unlike conventional construction, our oil and gas storage buildings feature seamless fabric envelopes that create an airtight environment when required, helping maintain safety standards while protecting materials from environmental exposure.
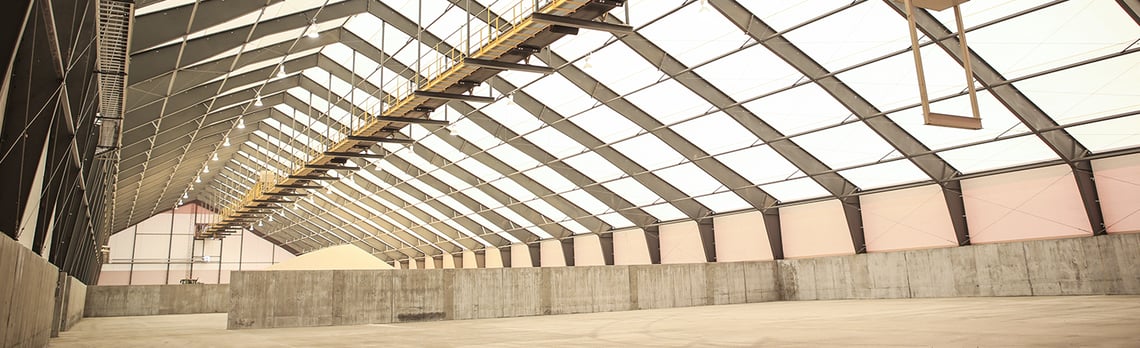
Our Process
Your dedicated project manager ensures every stakeholder's needs are met—from architectural vision to installation practicality—keeping your project on schedule from day one.
Our in-house engineering team works directly with designers and manufacturing, resolving potential issues before they become costly delays. This means faster approvals and fewer change orders, saving you both time and budget.
Every component of your building is manufactured in our 87,000 sq ft facility in St. Cloud, MN, under rigorous quality controls. This eliminates supply chain delays and ensures every component arrives on-site ready for installation.
Whether you opt for expert oversight of your local crews or our full-service installation team, you get our proven safety protocols and quality guarantees. Both options include on-site support to ensure your building is completed to specification and on schedule.
REAL-WORLD SUCCESS IN OIL & GAS
Biomethane Production Office & Processing Building
19,200 sq ft Biomethane Waste-to-Energy Production Building
The Biomethane Facility features a tall peak for tipping trucks, a sealed envelope to contain odors, and clear-span space to store food waste for use.
View Case Study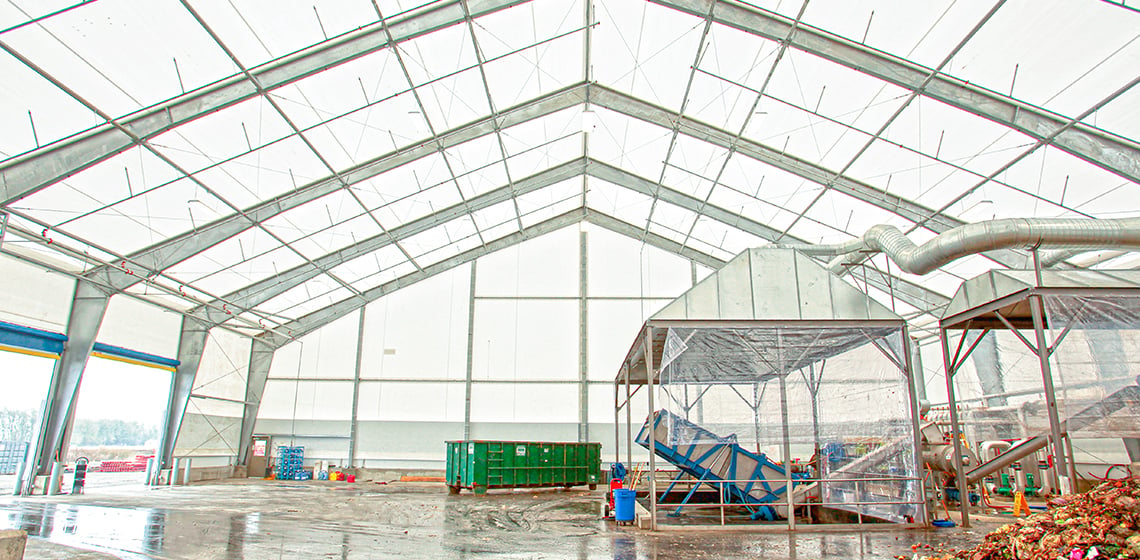
AGC Elizabethtown KY | Automotive Storage Solutions
16,482 sq ft Automotive Storage Structure | Elizabethtown, KY
AGC Elizabethtown KY - Explore our durable fabric structures for automotive storage.
View Case Study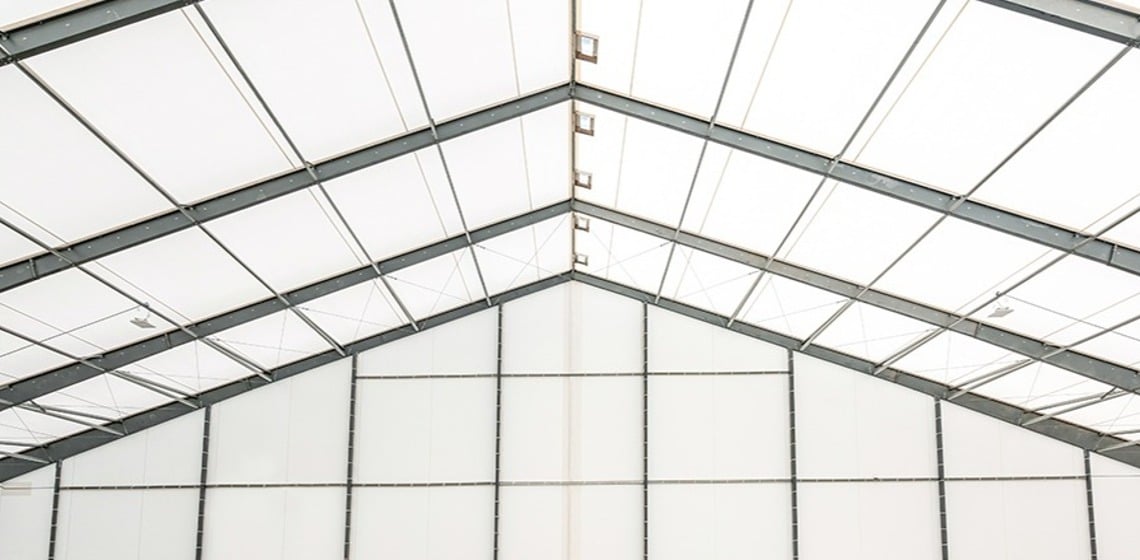
Basin Electric Power Cooperative Bottom Ash Dewatering Facility
52,800 sq ft Coal-Fired Energy Plant Processing Remediation Building | Stanton, ND
The structure, built over a wastewater facility, protects equipment dewatering ash and features a ventilation system with six air replacements per hour.
View Case Study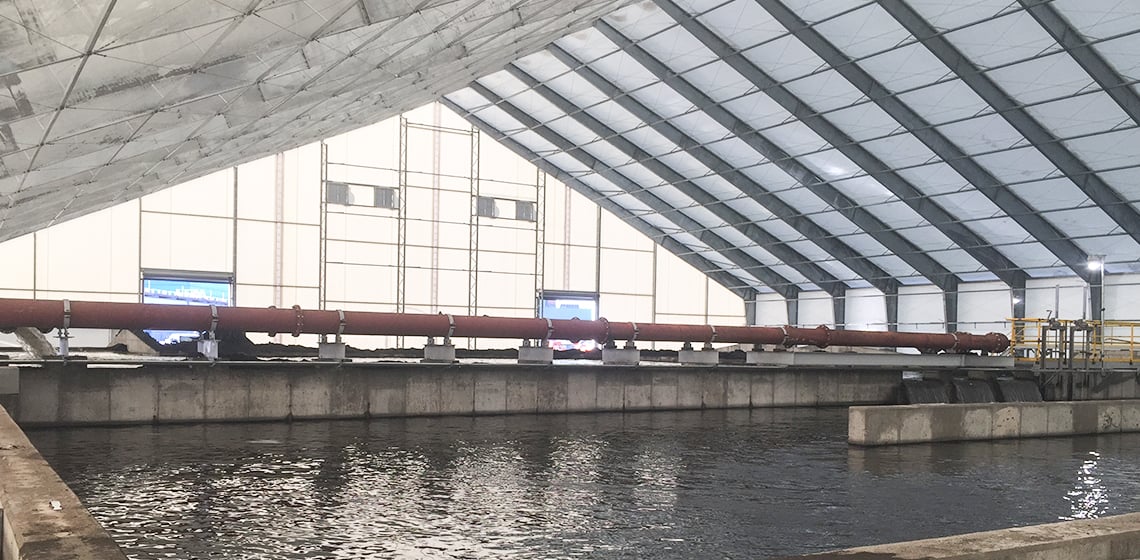
BBE Hydro Vehicle Maintenance and Warehouse Buildings
30,800 sq ft Vehicle Maintenance and Warehouse Buildings | Thompson, MB
Explore BBE Hydro's project in Thompson, MB, serving the mining, oil, gas, and energy industries. Subscribe to our newsletter for more updates!
View Case Study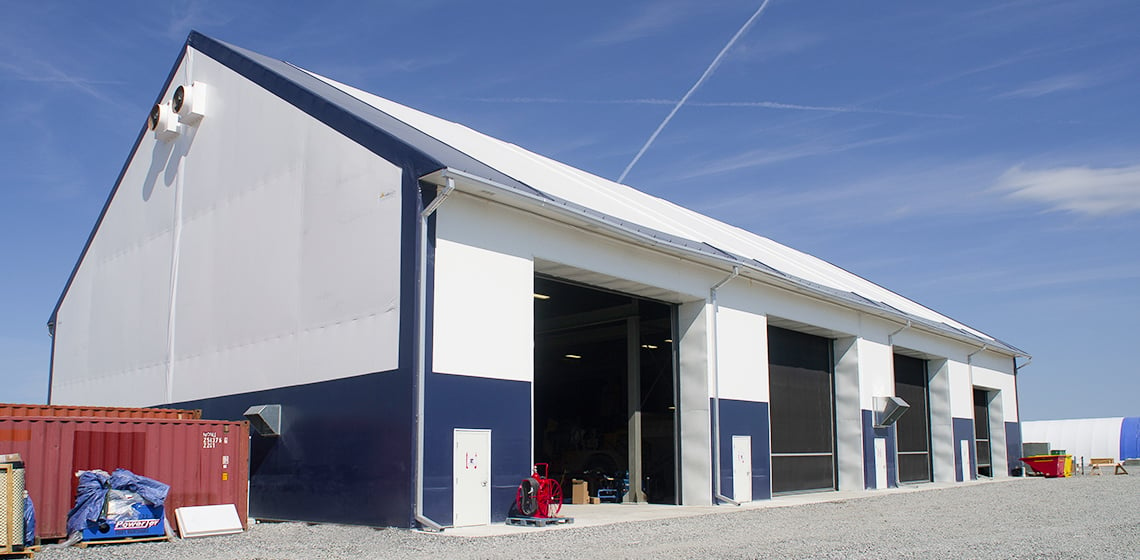
Montezuma Manufacturing Warehouse
9,600 sq ft Automotive Component Manufacturing Warehouse | Montezuma, IA
This automotive warehouse features straight walls, a tall peak for racks, and a gutter system to manage water and protect the foundation.
View Case Study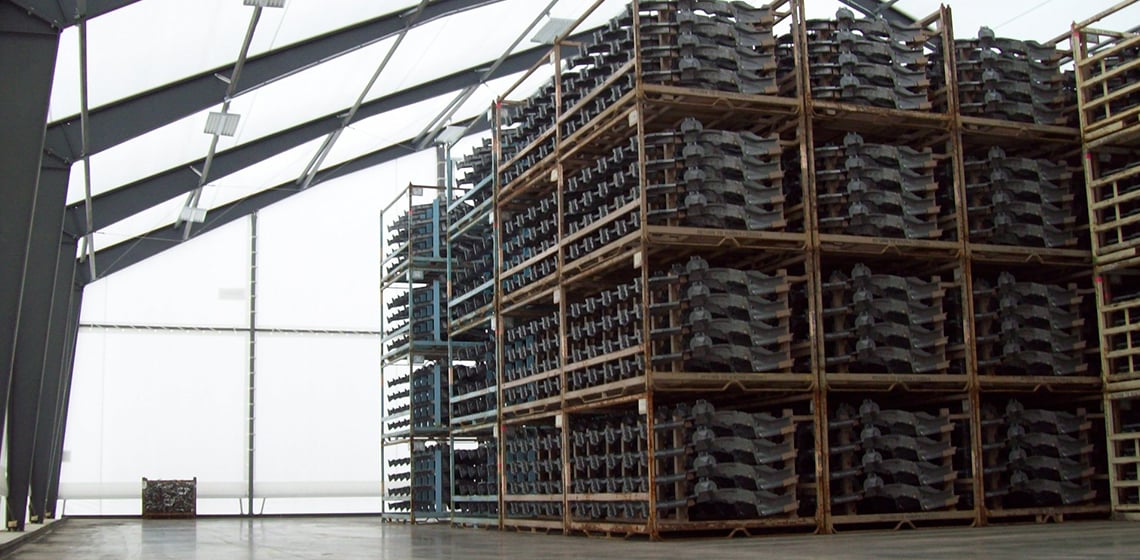
North Dakota LNG Co.
6,860 sq feet Liquefied Natural Gas Processing
North Dakota LNG Co. facility in Tioga, ND: 6,860 sq ft, Class 1/Div. 2 compliant, 41 ft peak clearance, custom foundation, ventilation, and doors.
View Case Study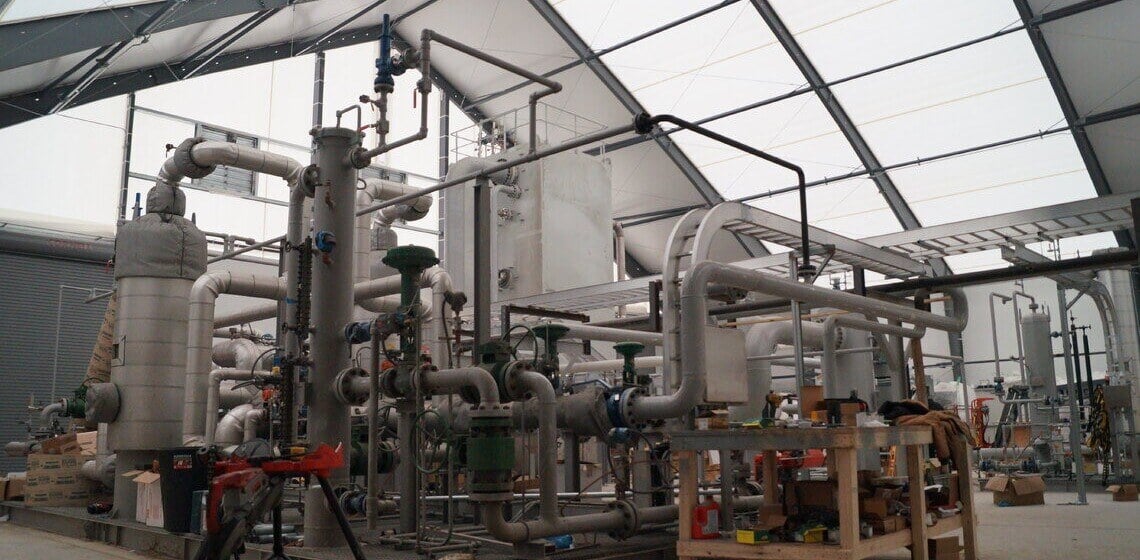
Testimonials
We had a great working relationship with Legacy
A lot of the temporary structures in the region are fabric structures, so we mainly looked at those types of buildings. Due to the overall project timeline, the buildings had to be constructed in the dead of winter. We had a great working relationship with Legacy throughout the entire process. They supply a very high quality fabric structure, and we're certainly pleased with what we've seen from the buildings thus far.
It was a seamless process.
The crew was so professional, polite, on time and hardworking. It was amazing to see how much they got done. There were weather delays and they still finished early. It was a seamless process, and a pleasure to work with this group.
We were very impressed by their engineering team.
By today's standards, the buildings we're designing are of world-class caliber in the U.S. and Canada. Legacy offered several features that put them at the top of the list. They are unique among fabric buildings in that they build on a rigid steel frame. Everything looked good, from the eave and ridge ventilation system to the method for installing fabric panels. Combined with material delivery times and the time to construct, Legacy seemed like the perfect choice for our application. "The whole design is very efficient for our operations. Flexibility is key, especially when the building is a 'first of its kind' for the industry. We had one design change after the whole plan was in place, to widen our trapeze in the structure that supports the conveyor, and Legacy was able to make that change without any problem. The conveyor system fits and operates just as it was designed. "Legacy knew our schedule and saved us over 30 days of downtime. They stood the frames for the entire fabric structure in a single day, and everything - conveyors, electrical, fabric - was completed within five weeks of them coming to the site. It was a Herculean effort on Legacy's part. It was fantastic. They have a very passionate team, from top to bottom. In all respects, from design to pricing to production, Legacy is one of the best building contractors I've ever worked with. I look forward to working with them again.
Start Your Project
Turn Your Vision into Reality—Faster
Get expert guidance on your facility design, timeline, and budget. Our team will help you reduce construction time, lower ongoing operational costs, and meet all environmental and safety requirements.