Ports & Waterways
.jpg?width=1140&height=450&name=Ports-DeLong-1%20(1).jpg)
Stronger, Faster, & More Cost-Effective Marina & Vessel Storage
Ports and waterways infrastructure requires buildings that can withstand harsh marine environments, adapt to evolving operational needs, and be constructed on tight schedules without exceeding budget constraints.
Whether you're an architect balancing structural integrity with design considerations, a general contractor coordinating materials and labor, or a business owner optimizing operations, the challenges are complex—but the solutions don’t have to be.
From marina storage buildings that protect watercraft year-round, commercial boatyards, inland ports, international seaports, or military amphibious craft to spacious yacht storage facilities that accommodate vessels of any size, our custom-engineered fabric structures provide the ideal solution for waterfront operations.
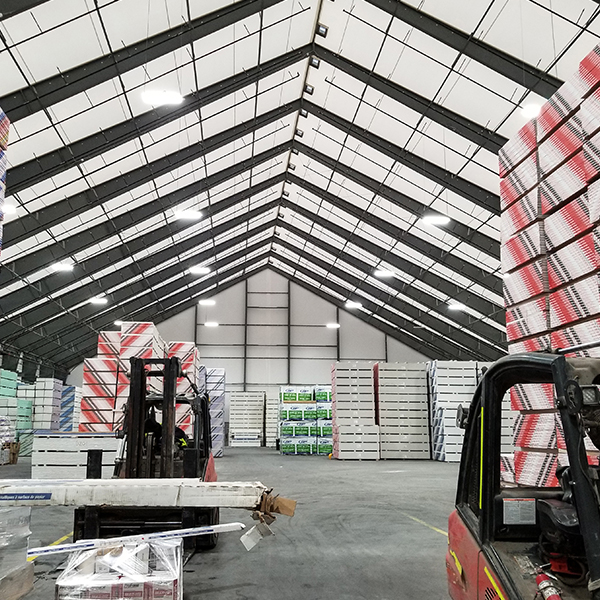
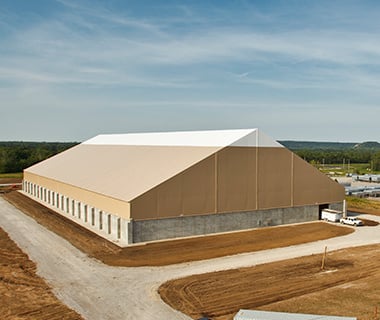
Withstand Harsh Conditions
Our custom-designed buildings provide corrosion-resistant materials that endure marine conditions, fast installation to minimize downtime and delays, cost-effective alternatives to traditional steel or concrete buildings, and clear-span interiors for unrestricted movement of goods and equipment.
With a focus on durability, efficiency, and customization, Legacy fabric structures help keep your operations running smoothly and your projects on track.
HOW LEGACY FABRIC CAN HELP
Purpose-Built Vessel Storage Solutions
Boatyard storage requires specialized structures that can withstand coastal elements while providing easy access for maintenance and repairs. Our fabric buildings offer the perfect balance of protection and accessibility for vessel storage of all types.
Whether you're developing marina storage facilities for seasonal customers or yacht storage structures for high-value watercraft, our buildings deliver the clear-span space and corrosion resistance that maritime operations demand.
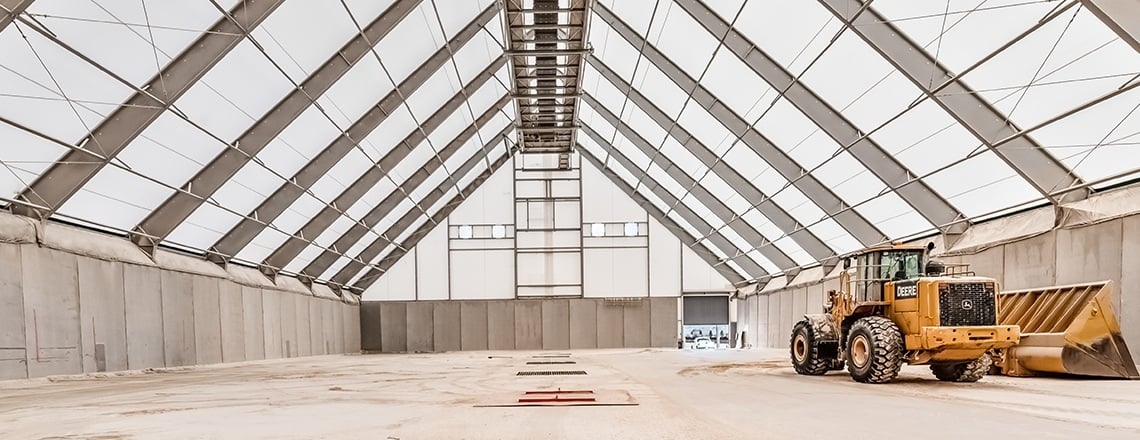
Corrosion-Resistant Materials
Ports and waterways facilities operate in some of the harshest conditions, with constant exposure to salt air, humidity, and extreme weather. Unlike traditional steel buildings that are prone to rust and degradation, our fabric structures are engineered with EpoxxiShield™ corrosion-resistant materials that won’t corrode over time.
This means lower maintenance costs, a longer lifespan, and increased structural integrity, ensuring your facility remains operational and durable for decades—without costly repairs or replacements.
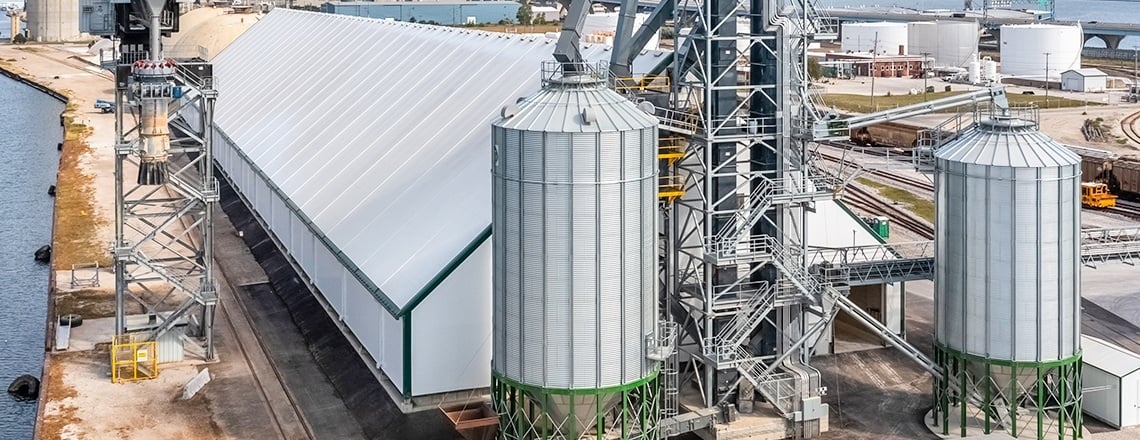
Faster Installation, Minimal Disruptions
Construction delays can disrupt port operations, leading to costly inefficiencies and missed deadlines. Our pre-engineered fabric buildings are designed for rapid installation, significantly reducing construction time compared to traditional methods. With clear-span interiors and modular components, our structures can be installed in weeks instead of months, allowing you to get back to business faster.
This accelerated build time minimizes downtime and labor costs, making it an ideal solution for fast-tracked infrastructure projects.
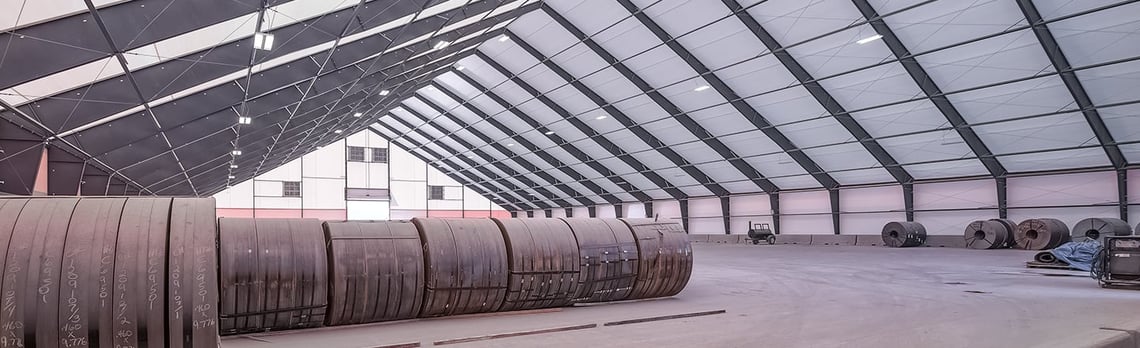
Cost-Effective Alternative to Steel & Concrete
When budgets are tight, decision-makers need a solution that offers strength and performance without excessive costs. Legacy’s fabric buildings provide the durability of traditional materials at a lower price point, reducing both upfront investment and long-term maintenance expenses.
Plus, with energy-efficient insulation options and natural daylighting features, our structures help lower operational costs, creating a more sustainable and cost-conscious facility.
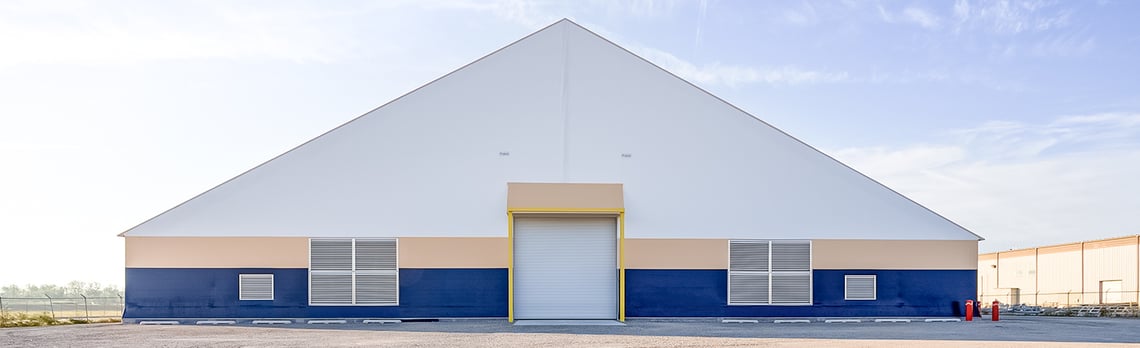
Clear-Span Interiors for Maximum Efficiency
Port and waterways operations require unobstructed space to move goods, store materials, and accommodate heavy machinery.
Legacy's fabric structures feature customizable, clear-span designs up to 300 feet wide, eliminating the need for interior columns or supports that can interfere with vessel movement and storage. With more usable square footage, vessel storage becomes more efficient and flexible—ensuring your marina storage facility is designed for optimal capacity and accessibility.
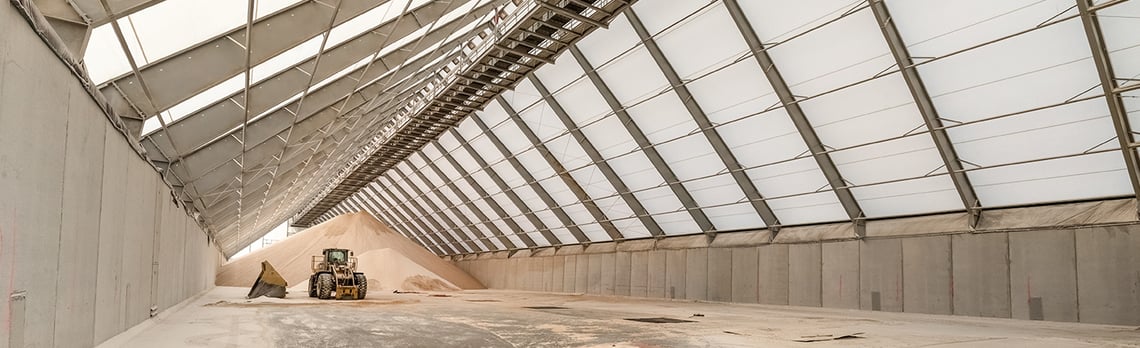
Built to Withstand Extreme Weather
High winds, heavy snowfall, and coastal storms pose serious risks to port infrastructure. Our fabric buildings are designed to meet or exceed all local and international building codes, ensuring they withstand extreme conditions.
With a flexible yet highly durable design, Legacy structures offer superior resilience against severe weather, keeping your operations protected year-round.
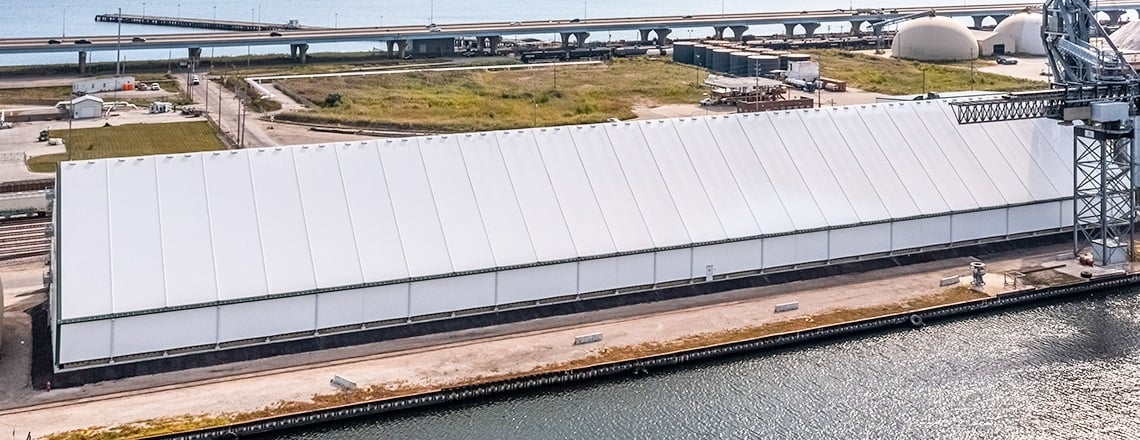
Our Process
Your dedicated project manager ensures every stakeholder's needs are met—from architectural vision to installation practicality—keeping your project on schedule from day one.
Our in-house engineering team works directly with designers and manufacturing, resolving potential issues before they become costly delays. This means faster approvals and fewer change orders, saving you both time and budget.
Every component of your building is manufactured in our 87,000 sq ft facility in St. Cloud, MN, under rigorous quality controls. This eliminates supply chain delays and ensures every component arrives on-site ready for installation.
Whether you opt for expert oversight of your local crews or our full-service installation team, you get our proven safety protocols and quality guarantees. Both options include on-site support to ensure your building is completed to specification and on schedule.
REAL-WORLD SUCCESS IN PORTS & WATERWAYS
Five Rivers Sand and Salt Storage
64,200 sq ft Salt and Sand Storage Buildings | Van Buren, AR
In 2014, Five Rivers Distribution added a 15,000 sq ft Legacy fabric building in Van Buren, AR, to store bulk materials like feed, salt, and fertilizer.
View Case Study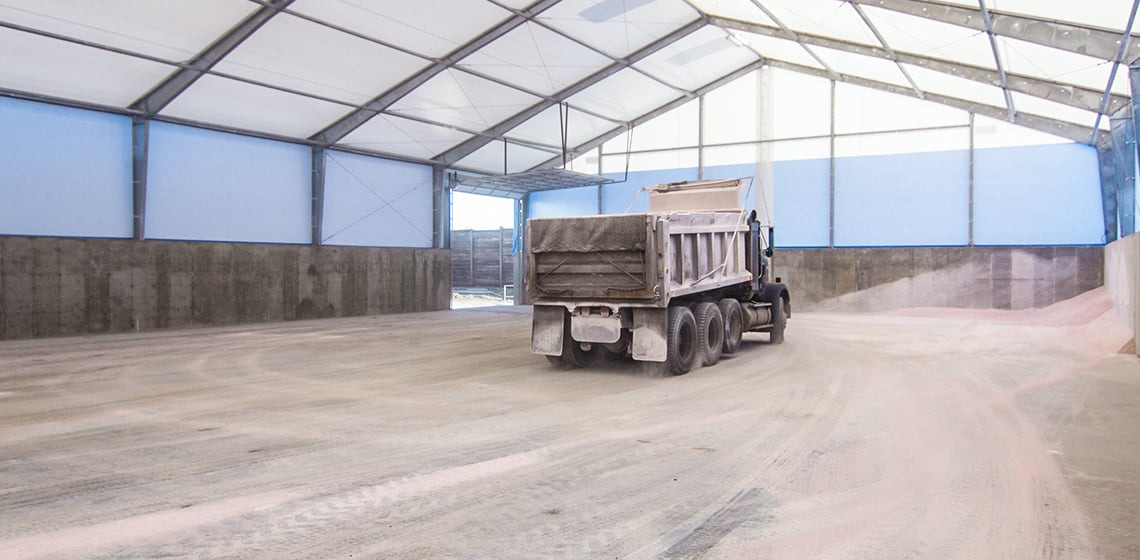
Duraport Marine and Rail Terminal Warehouse
51,360 sq ft Drywall Storage Building | Bayonne, NJ
DuraPort Marine and Rail Warehouse features a 51,360 sq ft Legacy fabric building with a concrete foundation, providing durable cold storage for operations.
View Case Study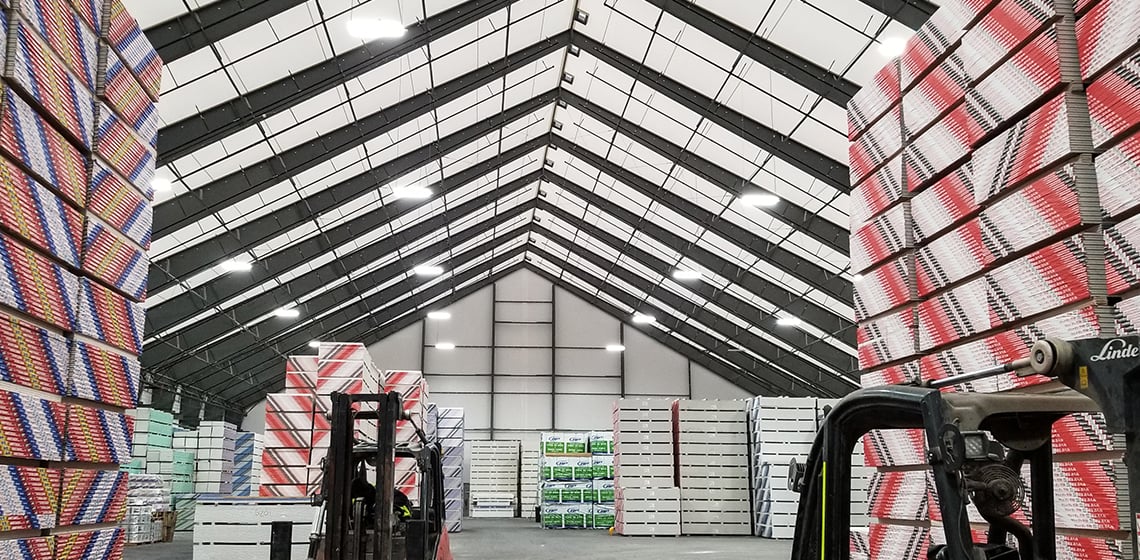
IEI Barge Services Storage Building
63,010 sq ft Tension Fabric Building for Fertilizer Storage and Blending | East Dubuque, IL
In 2015, IEI Barge Services chose Legacy’s lightweight design for a fertilizer storage building, solving soil and corrosion challenges affordably.
View Case Study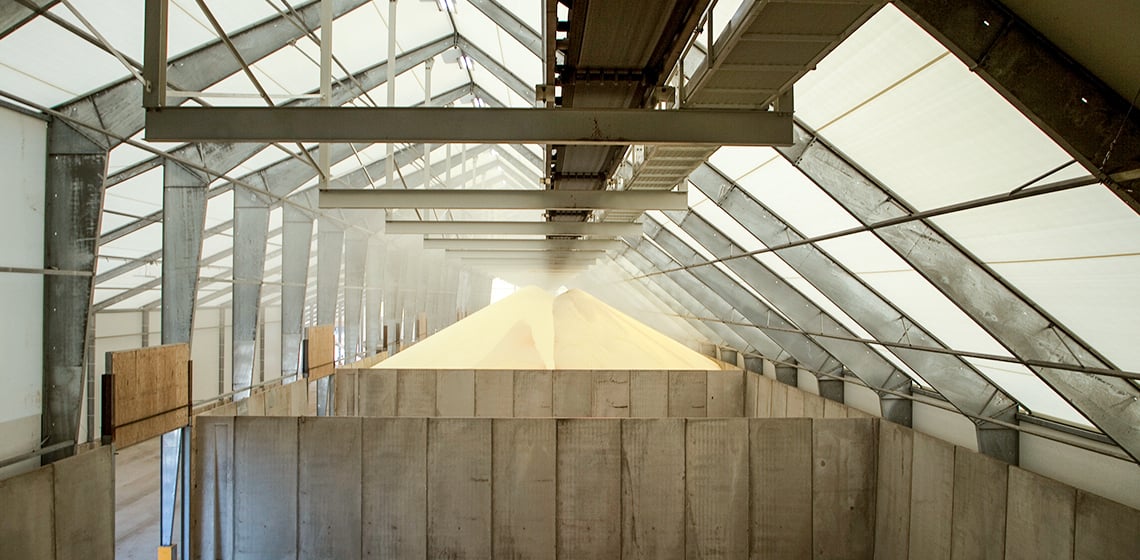
New Yard LLC Marine Storage Building
19,200 sq ft Marine Storage Building | Portland, ME
This Portland, ME facility stores boats with insulated walls, climate control, and natural light from roof panels for optimal protection.
View Case Study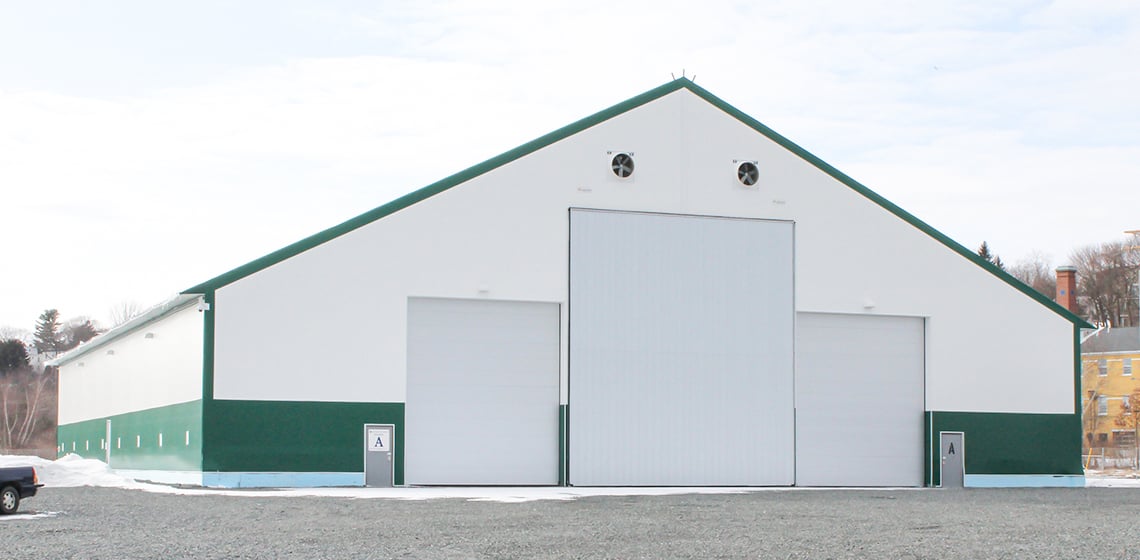
The DeLong Company, Inc.
69,600 sq ft DDGS Storage Facility
The DeLong Company and Legacy built a 69,600-ft DDGS export facility, opening Wisconsin to new agricultural markets.
View Case Study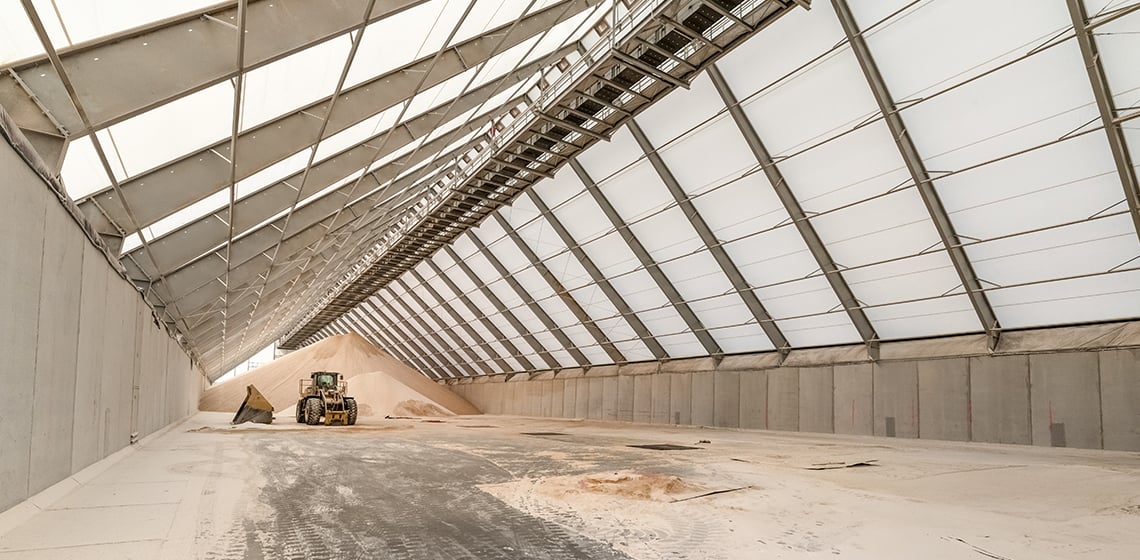
Testimonials
The new building will protect the salt supply.
It will be protected from being compromised by wind and precipitation. Once the general contractor completed the footings and floors, Legacy installed the fabric building very quickly, in about two weeks. It was a very positive process with professional communication between Legacy and Dewberry throughout the project.
Everything that Legacy said they were going to do, they did.
We obviously had contracts, but the overall feel was kind of like the olden days, where you felt you could just take somebody at their word. Price is a major factor in any purchase decision. But we didn't blink at having to pay a little more for the Legacy structure. Sometimes you have to spend more to get a higher quality building. The installation was very smooth. Legacy's in-house crew worked in cold winter conditions, and they erected the building within five days. They were a very professional group, and I'd highly recommend them. We like the sidewall columns going straight up instead of curving down like in our hoop buildings. First off, it lets us put more product in there. And our front-end loaders can get much closer to the walls and drive straight down the sides. It gives us more working room and increases our efficiency. In the long run I think this will be a building that requires less maintenance. Legacy was so outstanding to work with that I didn't even bother looking at pricing elsewhere.
The Legacy construction crew was very professional and courteous.
Because of our soil issues, we simply couldn't afford to construct a more traditional building. The concrete costs made a more traditional building cost prohibitive. The lightweight design of our Legacy building allowed us to reach a compromise between soil conditions and cost. Regarding the design and construction phases of the building, I can say that the process went exceptionally well. When I made eleventh-hour changes to the job, Legacy handled them with ease. They finished the job well ahead of schedule, worked safely, and followed our stringent safety requirements to the letter.
Start Your Project
Turn Your Vision into Reality—Faster
Get expert guidance on your facility design, timeline, and budget. Our team will help you reduce construction time, lower ongoing operational costs, and meet all environmental and safety requirements.